1. Drilling preparation
The drilling angle, length, mix ratio of slurry, and selection of drill bits should be determined according to the rock formation. Most tunnel advance support will use 51, 76 self-propelled bolts. Adjust the drilling angle of the rock drill according to the terrain and geological conditions.
2. Drilling and grouting
When the Self-Drilling Anchor bolts is long and needs to be spliced, the drill bit should be put on the front end of the first section of the anchor rod, and the tail end of the rod body should be connected to the grouting machine through the rotary grouting adapter. When drilling, grouting is carried out, and the slurry is pressed into the hole and into the cracks of the rock mass to consolidate the rock mass and stay in the deep stable rock mass, and bond together with the stable layer as the slurry solidifies.
3. Anchor rod connection length
When there is 30cm left in the first section of the anchor rod, stop drilling, put a connecting sleeve with artificial lubricant on the tail of the previous section of the anchor rod, and then connect the second section of the anchor rod, and so on, until the drilling reaches Design length. At the end of the drilling, the anchor rod is exposed at least 10cm, which is convenient for installing the arched backing plate and the ball nut.
4. Pull test
After the construction of the self-propelled bolt, the pull-out force value test of the bolt should be carried out to check whether it meets the design value of pull-out force. For every 300 bolts in the operation area, no less than 3 bolts should be randomly checked for pull-out force test to ensure that the construction effect meets the expected requirements.
The above is the answer to the question of how to support the tunnel crossing the pebble layer. The quality of the support affects the safety of the tunnel construction. It is necessary to adopt supporting materials with rich successful supporting cases and rich construction case verification.
The Self-Drilling Anchor bolts produced by Jiufu have many tunnel application cases, and can provide customers with a complete set of solutions. You are welcome to inquire.
For many manufacturers, we are not only recognized by our customers for our high-quality products, but also very good in detail services. Our product packaging will be different according to the surface treatment of the product and the way of transportation. For the self-drilling anchor bolts that have not been surface-treated, we will use a rain cloth for packaging to prevent corrosion and rust by seawater during transportation. For the self-drilling anchor bolts that are hot-dip galvanized and epoxy-coated We will take the packaging method to facilitate transportation and loading and unloading. We are proud that these packaging will be provided to customers free of charge.
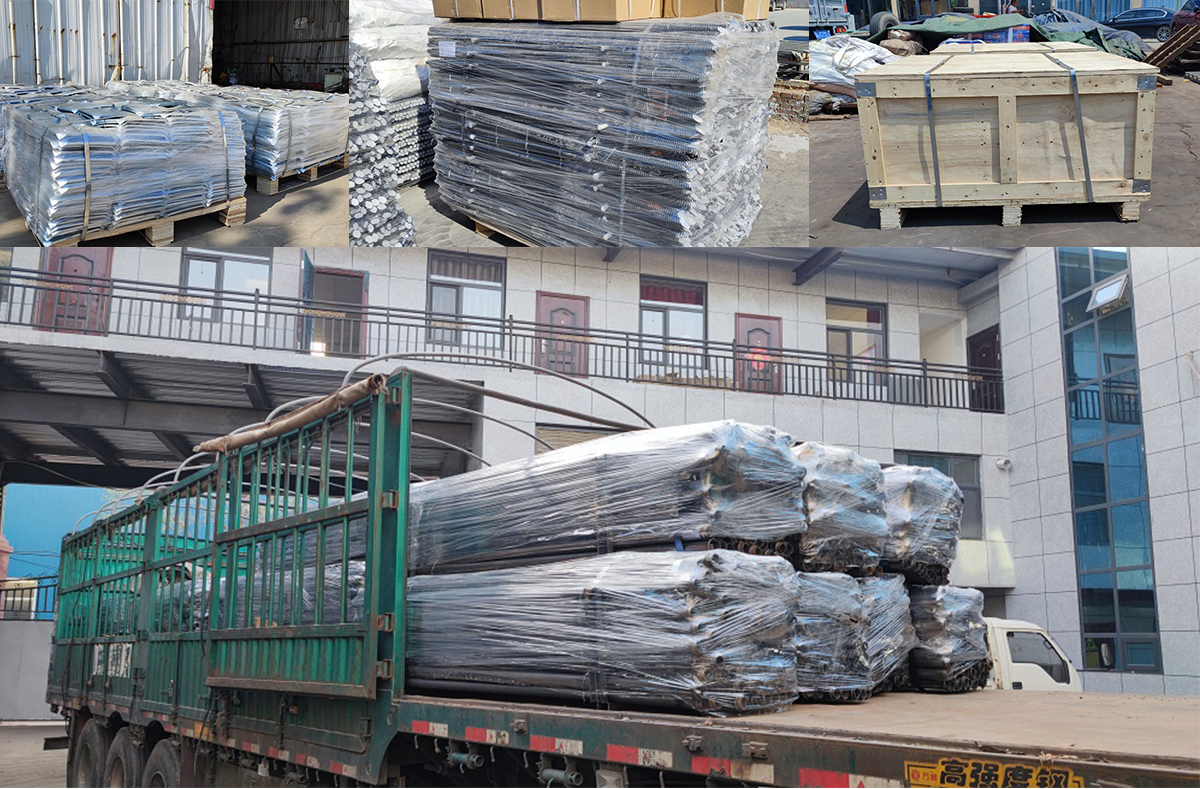